Can the steel industry ever go green?
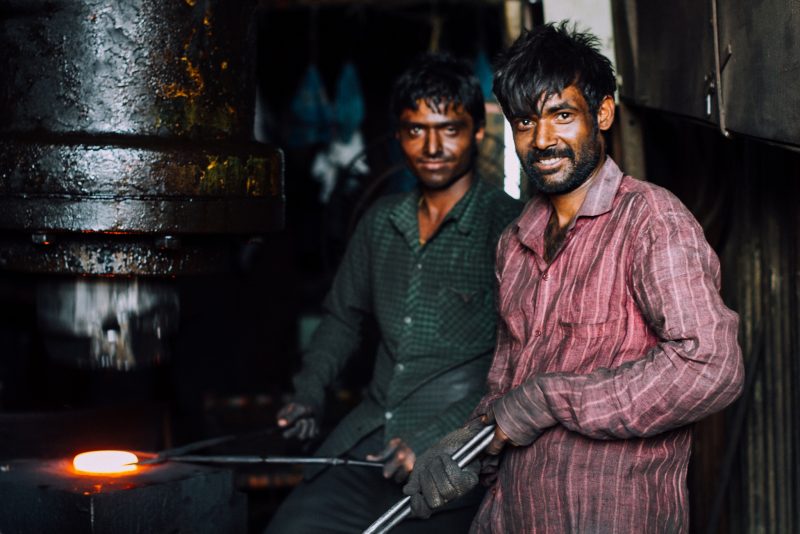
It's not just electricity that uses fossil fuels and emits lots of carbon - heavy industries like steel also pose real challenges to green economy policymakers. What can be done?
The steel industry is one of the major contributors to global CO2 manmade emissions - about 2.75Gt, or 6-7% of the total. Cement is not far behind. These two sectors are the giant emitters, way ahead of other industrial sectors. They are, of course, dwarfed by the power sector and the automotive sector, but together the two are a very important part of the CO2 problem.
But what is worse is that there are no obvious technological solutions, certainly for steel. About 90% of the sector’s emissions come from primary steelmaking, which for 150 years has required a carbon-intensive process, using metallurgical coal to reduce iron ore into hot metal. Scrap-based steelmaking emits much less CO2, directly or indirectly, but there is not enough scrap to support more than 30% of the world’s 1.5bnt of steelmaking. It is possible to imagine a Circular Economy in Steel, but it will not happen for decades, and not even in the mature economies of Europe or Japan: this is because steel stays embodied in infrastructure for a very long time.
Why should a Green Economy need steel at all? What about other materials? Unfortunately most other materials also come with a heavy carbon footprint - aluminium, plastics, carbon fibre. Timber is a promising substitute for some uses in construction, but only some uses and the availability of timber of obviously restricted by land-use constraints.
Could we use much less steel? Half of the world’s steel consumption is in China, where the dominant use is in construction - infrastructure, residential, commercial. Successive five year plans may reduce the steel intensity of the economy, but only gradually. In developing and emerging economies over half of steel consumption is for construction, and will be for decades to come. In mature economies the most important role for Steel is in the manufacturing sector, where steel intensity is falling but where steel remains essential.
If steel is essential to the world as we know it, could we decarbonise steelmaking? So far we do not know if we can. About 15 years ago Francis Mer, then CEO of Europe’s leading steel company, Usinor, initiated a programme in Europe, where, under the title ULCOS, leading European steel companies and technology companies cooperated, with financial support from the European Commission, in a series of R&D initiatives designed to reduce radically the carbon footprint of steelmaking. The programme ran from 2004 to 2014, and as it evolved focussed on four main processes, three of which would need to be supported by Carbon Capture and Storage (CCS) to achieve major decarbonisation.
One of these processes, HISarna is still running on and off by Tata Steel in the Netherlands, but with limited financial support. Another, which enjoyed a small successful pilot programme, was to have involved a demonstration project in France costing about €500m, but this was aborted on the grounds of cost and technological risk. Meanwhile the Japanese steel industry have had R&D projects to try to develop hydrogen steelmaking.
An alternative approach, being investigated by Julian Allwood and colleagues at Cambridge, is to find ways of using much less steel through much more intelligent design (e.g. of buildings) and much more effort to reuse. This could reduce the need for new steelmaking, but only to a limited extent.

Innovation and investment
At present the steelmaking processes used throughout the world derive from innovation initiated in Europe and Japan. If the Chinese steel industry seeks to modernise it will primarily look at technologies first developed in Europe and Japan. But none of these technologies today do much towards a radical decarbonisation of the industry.
For Europe there are three main routes to follow: the processes developed under the ULCOS programme linked to CCS; hydrogen steelmaking, now being looked at by steelmakers in Sweden, Austria and Germany, and electrolysis. All of these will require substantial public support, for R&D, for demonstration projects, and probably to compensate for higher costs for operation.
But there is little or no public support available. The EU Horizon and Innovation programmes may do something on a small scale. But in general the steel industry struggles to make its case, and its low profitability makes it unwilling to invest much in long-term, speculative, probably higher-cost technologies. And no level of carbon pricing foreseeable in the short or medium term can give enough incentive to companies to invest in such transformational change.
In countries like the UK which may now want to rebalance their economies to assist their rustbelts this is a challenge and an opportunity - and a potential large cost. The UK has the advantage of the best access of any European country to the North Sea, whose geology is well-suited to CCS; however any cost-effective pursuit of CCS has to involve a hub to serve a number of sectors, including power - a further opportunity for beleaguered industrial Humberside and Teesside? By contrast Germany tends to be sceptical about CCS on the grounds of public acceptability of CCS inland - but if it pursues hydrogen steelmaking then it will have to find a carbon neutral method of generating hydrogen.
Or we could do nothing, and assume that steelmaking can never be green, and that its inevitable gigatonnes of carbon emissions will be compensated later in the century by negative emissions in other sectors. Probably a risky assumption. Hence the case for a focus on this sector, and for public support now for trying to green this very mature and carbon-intensive process.
Chris Beuaman, European Bank of Reconstruction and Development (EBRD)
Photo credits:
"Steel Workers Forging Steel, Mumbai" (CC BY-NC-ND 2.0) by AdamCohn
"Steel Worker Houston Texas 1" (CC BY 2.0) by billjacobus1